Methodology for investigating the Complaints
The following procedure will help in investigating the customers’ complaints. According to OSHA, written complaints must be received prior to investigations. Thus, the first step will be to review the complaint records in order to determine whether the investigation should be given priority or not (WHSA 2011, pp. 18-162). Before starting the investigation, I will require information about the substances used in the salons.
This includes a list of the nail products or any chemicals used in the salons. During the investigations, I will need information about the toxicity of the substances used in the salons and the measures that have been taken to enhance safety. Finally, a report on the investigation will be necessary in order to classify the odor as hazardous or non-hazardous.
Risk assessment will be the first step in the investigation. The current MSDS for each product or substance used in the salons will be obtained from the manufacturers. The MSDS contains information about the concentrations of the ingredients of nail products. These concentration levels will be recorded and compared with the standards set by Safe Work Australia. The results will help in determining whether the nail products pose any health risks to the customers, workers and other shopkeepers. The second step will involve interviewing a sample of customers, workers and neighboring shopkeepers in order to understand how they are affected by the odor.
Finally, an inspection will be done in the salons and the adjacent shops. This will involve actual visits to the salons and adjacent shops, as well as, reviewing past health and safety inspection reports (Safe Work Australia 2012, pp. 5-31). The inspection will focus on the hygiene standards in the salons and the measures taken to minimize health hazards. A low hygiene standard is an indication that the complainants are at risk of being affected by the odor. Last and most importantly, the inspection will help in verifying the existence of the odor.
Methods for Identifying the at Risk Persons
Health and safety audits are normally conducted at workplaces in order to identify hazards and the persons who are likely to be affected. This can be achieved through the following criteria. To begin with, the audit must focus on identifying the stakeholders who are likely to be affected by the hazard (Reolofs & Do 2012, pp. 2-7). In our case, the people who are directly or indirectly involved in the operations of the salons are likely to be affected by the odor.
Customers and workers are the stakeholders who are directly involved in the operation of the salons. The workers are at a high risk of being affected since they are exposed to the chemicals and procedures that produce the odor for a very long time.
Similarly, the customers are at risk since their visits to the salons expose them to the odor for a relatively long time. The chemicals used in nail salons usually produce fume, vapor, as well as, dust which can be toxic. These byproducts usually affect customers and workers through inhalation and skin contact or absorption. The general public and neighboring businesses are also at risk of being affected since odor spreads through the atmosphere, and its effects can be felt outside the salons.
Having identified the at risk persons, it will be necessary to determine the hazard they are exposed to. Concisely, it will be necessary to determine if the odor is just a nuisance or if it is hazardous. Most of the ingredients used in nail products are toxic (Reolofs & Do 2012, pp. 2-7). The main chemicals or ingredients in nail products include ethyl methacrylate and methacrylic acids. Empirical studies have reported mixed results on the toxicity of these chemicals.
In some studies, these chemicals have been found to be highly toxic, and thus, should not be used to manufacture cosmetics. However, some studies have found little evidence of high toxicity in these chemicals. Thus, in order to determine whether the odor is a health hazard or not, it will be necessary to measure the toxicity of the chemicals associated with it. The measurement will focus on the concentration of the toxic chemicals. The results will be compared with the acceptable concentration standards.
The following procedures will help in determining the toxicity of the odor. First, short air quality audits will be done in the two salons and the neighboring shops. Due to the large size of the shopping center, only a few businesses will be selected for the audit. A random sample will be used to identify the businesses that will participate in the audit. However, priority will be given to the shops which are adjacent to the salons since they are likely to be the most affected.
The audit will be used to collect information on air quality, availability of air conditioners and natural ventilation. Furthermore, the humidity, temperature and the level of carbon dioxide concentration in the salons will be measured. These measurements will be done with the aid of calibrated TSI Q-Track monitor. The level of carbon dioxide concentration can be used to estimate the quality of air in the salons. The natural level of carbon dioxide concentration in an open space is usually 300-600 ppm (Reolofs & Do 2012, pp. 2-7). Thus, any concentration that is significantly different from this level will be an indication of poor air quality in the salons.
Second, tests will be conducted on biological, as well as, workplace samples in order to determine the severity of the harm caused by the odor. The biological measures include blood and urine samples which will be obtained from the customers, workers at the salons and other shopkeepers. The samples can be collected from the shopkeepers immediately after each day’s shift or at the end of the week.
For customers, the samples can be collected immediately after visiting the salons. Samples of air, dust and vapor will also be obtained from the salons and shops. These samples will be analyzed in order to detect the presence of any toxic substance that can be directly linked to the odor that emanates from the salons. Due to the technical nature of the tests, the analysis will be done by the Chemical Analysis Branch (CAB).
This organization is accredited by the National Association of Testing (NATA), and it specializes in the provision of occupational health analytical services (Chemical Analysis Branch 2012, 5-44). Thus, the results obtained from CAB are likely to be reliable. Based on these results, we can obtain quantitative data such as the concentration of toxic chemicals and the number of affected customers or shopkeepers.
Third, exposure assessments will be done in the salons and selected shops in the shopping center. The assessment will help in characterizing exposure to the odor, the intensity of the odor, as well as, the potential health risks. Consequently, it will be possible to confirm if the odor is hazardous or not. Exposure assessments focus on the factors that influence the concentration of contaminants (NSW Government 2012).
These factors include toxic substances, workplace processes, engineering controls and the environment (WHSR 2011, pp. 30-400). Our assessment will focus on the odor and its effects on the customers and shopkeepers. Hence, the assessment will attempt to highlight the aspects of the odor such as the number of people it affects, its rate of generation and the environmental factors that exacerbate its effects.
For instance, the odor is likely to affect more people on a windy day. Moreover, we can determine the variability of the odor through the exposure assessments. For example, if the intensity of the odor is high during the day, then most shopkeepers are likely to be affected. This is because many shops are normally open during the day than in the night.
Methodology for Evaluating the Monitoring Data
Statistical techniques will be used to evaluate the collected data. These techniques will be used as follows. To begin with, random samples of the customers, shopkeepers and workers at the salons will be selected. A random sample approach helps in avoiding bias in the selection of participants (Lind & Nenonen 2008, pp. 194-204). The data collected from these samples will be analyzed with the aid of statistical formulae such as arithmetic mean, geometric mean, percentiles and standard deviation.
These techniques will be used to assess air quality variables such as temperature, humidity and carbon dioxide concentration in the salons and neighboring shops. The collected data will be taken to CAB for further analysis in order to verify the air quality in the salons and adjacent shops. The results will be compared with the air quality standards that have been set by Safe Work Australia. Additionally, the safety and hygiene standards set by the Work Health and Safety Act will be used to assess the salons’ hygiene standards.
Exposure standards refer to “the airborne concentration of individual chemical substances in the worker’s breathing zone which should not cause adverse health effects” (AIOH 2010, pp. 6-19). In our case, the standards will focus on the concentration of the toxic fume (odor) that is produced by the salons. The most commonly used exposure standards include “the 8-hour time-weighted average, peak limitation and the short-term exposure limit” (AIOH 2010, pp. 6-19).
The 8-hour time-weighted average (TWA) is the level of exposure to a given substance that is allowed within an eight-hour working day. This standard will be used to evaluate the collected data. Table 1 indicates the concentration of various ingredients of nail polish in the salons.
Table 1: Concentration of substances in the salons.
Table 2: Concentration of substances in neighboring shops.
Table 1 and 2 compares the actual concentrations of various substances with the recommended concentration standards (8-hour TWA). According to table 1, the customers are at risk since the concentration of the substances exceeds the recommended 8-hour TWA. Table 2 also shows that the neighboring shopkeepers are at risk since the concentration of most substances exceeds the 8-hour TWA. According to OSHA, butyl acetate concentration above 150 ppm is likely to cause headache, as well as, irritation in the eyes and skin (Reolofs & Do 2012, pp. 2-7).
Ethyl alcohol concentration above 400 ppm normally causes headache, dry/ cracking skin and irritation in the eyes and nose. These effects can also be experienced if a person is exposed to ethyl acetate concentration that exceeds 400 ppm. Thus, the customers, workers and other shopkeepers are at risk of experiencing these health conditions.
Measures for Controlling the Odor
Health hazards must be controlled at the workplace in order to minimize their potential harm to the workers, customers and the general public. According to the hierarchy of risk control, level 1 is the most effective means of managing any hazard. This means that the most effective way of controlling the odor is to eliminate it (Aziz 2010, pp. 67-82). In this context, the salons will have to stop using the nail products and the processes that generate the odor.
It is apparent that nearly all nail products are made of toxic ingredients. Furthermore, the salons cannot operate without the nail products. Consequently, elimination will not be possible. Eliminating the use of artificial nail products can lead to the closure of the salons. Besides, quite a number of customers will not be able to enjoy the nail art services. In this regard, level two and three tends to be the most practical and socially responsible measures.
Level two advocates for the substitution of the hazard with a less dangerous substance, isolating the substance and using engineering controls (Safe Work Australia 2012, pp. 5-31). In order to substitute the hazard, the salons will have to use nail products whose ingredients have low toxic concentrations. Thus, the salons must have information about the chemical composition of the nail products that they use.
This information can be obtained from the Hazardous Substances Information Systems (HSIS) database. Products whose ingredients are considered to be highly toxic should not be procured for use in the salons. It is important to involve the manufacturers of the nail products in the substitution process. Concisely, the manufacturers must be informed about the health effects of their products. Besides, they must be advised to use less toxic ingredients to manufacture the nail products (Kirsten 2008, pp. pp. 136-144).
The consumer protection laws must also be enforced to ensure that only safe products are used in salons. In this case, manufacturers whose products fail to comply with the safety standards should be penalized. Similarly, all salons found to be using any unsafe product should be penalized.
Isolating the hazard will involve restricting access to the nail products. This can be achieved by properly storing the products when they are not in use (Zwetsloot & Scheppingen 2010, pp. 143-159). Hence, the level of exposure to the products will reduce. This is the simplest and the most cost-effective control method. However, it is not likely to be effective in controlling the hazard. In most salons, nail products are always in use.
Thus, the possibility of having them kept during the working hours is very low. Using engineering controls will involve changing the design of the salons and the equipment or facilities used in them. Figure 1 shows a type of manicure table that can be used to replace the existing ones. This table facilitates automatic removal of any toxic dust or gases that are produced during the manicuring process (Chapman 1981, pp. 1-4). Moreover, it facilitates treatment of any harmful fumes or odor. The residuals of the treated fumes and dust are also removed from the ambient environment. Consequently, the customers, workers and other shopkeepers can not be affected by the fumes.
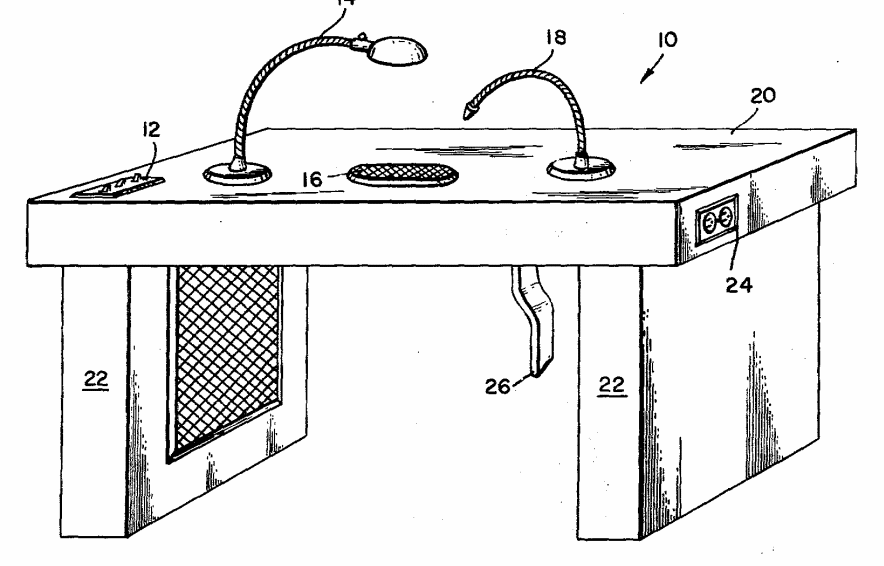
The nail sculpting station shown in figure 2 can be used by the salons to reduce the odor. Each of the workstations has a work surface (16), arm rests (18), as well as, an exhaust vent (20). The vents are used for the disposal of dust and fumes through a central exhaust duct (Bloom 1998, pp. 1-6). Consequently, the customers and the workers will not be affected by the fumes. Finally, figure 3 shows an equipment which can be used to control vapor emissions in salons.
The equipment consists of an isolation chamber which houses the vapor emitting materials. The vapor is filtered before it is removed from the chamber and released into the atmosphere (Pham 1992, pp. 1-6). Consequently, the customers, neighboring shopkeepers and the general public will not be affected by the fumes or odor. These facilities are likely to be effective since they are affordable and can significantly reduce the odor.
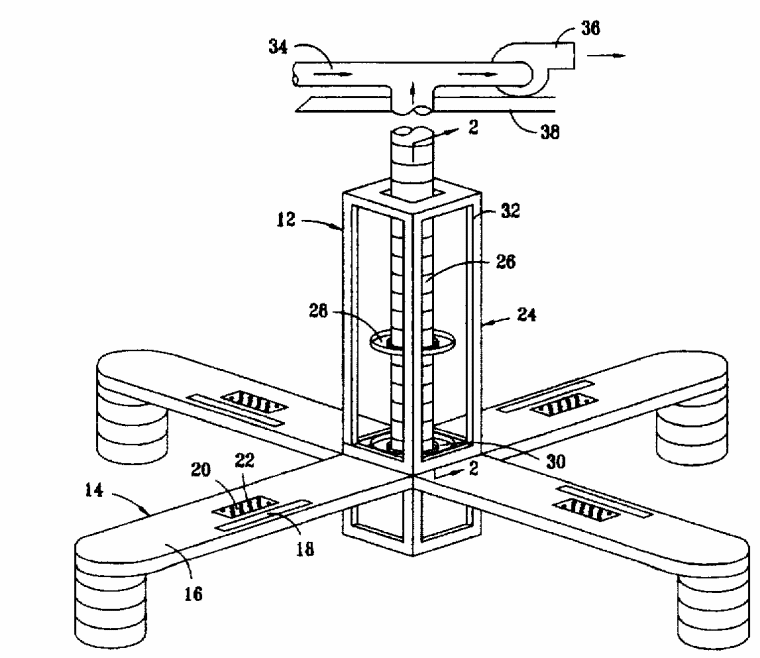
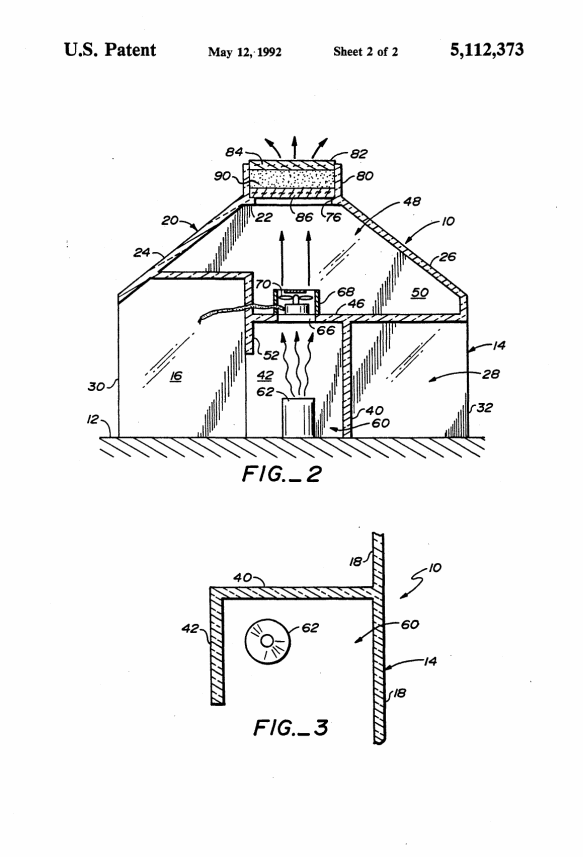
Level three involves using administrative measures such as providing information about the health hazards associated with the nail products. The stakeholders can also be informed about the symptoms of the infections caused by the odor (Roberts, Bowen & Barber 2011, pp. 335-340).
According to Reolofs and Do (2012) over 90% of nail salon workers have received training on health hazards. Additionally, 77% and 12.5% of workers in nail salons have shoulder and back problems respectively. Thus, they should be trained on how to offer first aid whenever signs of infections are detected. Finally, protective equipments such as dust masks should be used by the customers and shopkeepers to avoid being affected by the odor.
Methods for Evaluating the Efficacy of the Controls
Implementation of the aforementioned measures should be monitored and evaluated on a regular basis. The effectiveness of the measures can be illustrated by the extent to which they reduce the hazard. A significant reduction in the odor after the implementation of the measures implies that the controls are effective. The rate at which the controls are being adopted by the salons is also an indication of their effectiveness.
In this case, it will be necessary to find out the challenges that hamper the implementation of the measures. For example, the measures will not be implemented if they are too expensive. Finally, complain reports will be reviewed. In this case, a reduction in complaints from the customers and other shopkeepers indicates that the measures are effective.
References
AIOH 2010, Adjustment of Workplace Exposure Standards for Extended Work Shifts, AIOH, Tullamarine.
Aziz, B 2010, ‘The Effective Management of Occupational Health and Safety’, International Journal of Health Care Quality Assurance, vol. 6 no. 5, pp. 67-82.
Bloom, G 1998, Nail Polishing Workstations with Ventilation and Carousel Tray, University Park, Texas.
Chapman, V 1981, Environmental Manicure Systems, Peacock La, California.
Chemical Analysis Branch 2012, Information for People Wanting to Submit Workplace and Biological Monitoring Samples for Analysis, Work-Cover NSW, Tullamarine.
Kristen, W 2008, ‘Health and Productivity Management in Europe’, International Journal of Workplace Health Management, vol. 1 no. 2, pp. 136-144.
Lind, S & Nenonen, S 2008, ‘Occupational Risks in Industrial Maintenance’, Journal of Quality in Maintenance Engineering, vol. 14 no. 2, pp. 194-204.
NSW Government 2012, Identifying Hazards. Web.
Pham, H 1992, Apparatus for Controlling and Eliminating Vapor Emissions at a Manicure Work Station, Appian Way, California.
Reolofs, C & Do, T 2012, ‘Exposure Assessment in Nail Salons: an Indoor Air Approach’, Public Health, vol. 12 no. 1, pp. 2-7.
Roberts, H, Bowen, J & Barber, M 2011, ‘Worker-Related Symptoms in Nail Salon technicians’, Occupational Medicine, vol. 61 no. 5, pp. 335-340.
Safe Work Australia 2012, How to Manage Work Health and Safety Risks: Code of Practice, Safe Work Australia, Sydney.
WHSA 2011, Work Health and Safety Act, NSW Government, Sydney.
WHSR 2011, Work Health and Safety Regulation, NSW Government, Sydney.
Zwetsloot, G & Scheppingen, A 2010, ‘The Organizational Benefits of Investing in Workplace Health’, International Journal of Workplace Health Management, vol. 3 no. 2, pp. 143-159.